Meet the F-Bomb: the latest predator trap invention. Lightweight, simple and easy to use, is it the key for the wider public to get into trapping?
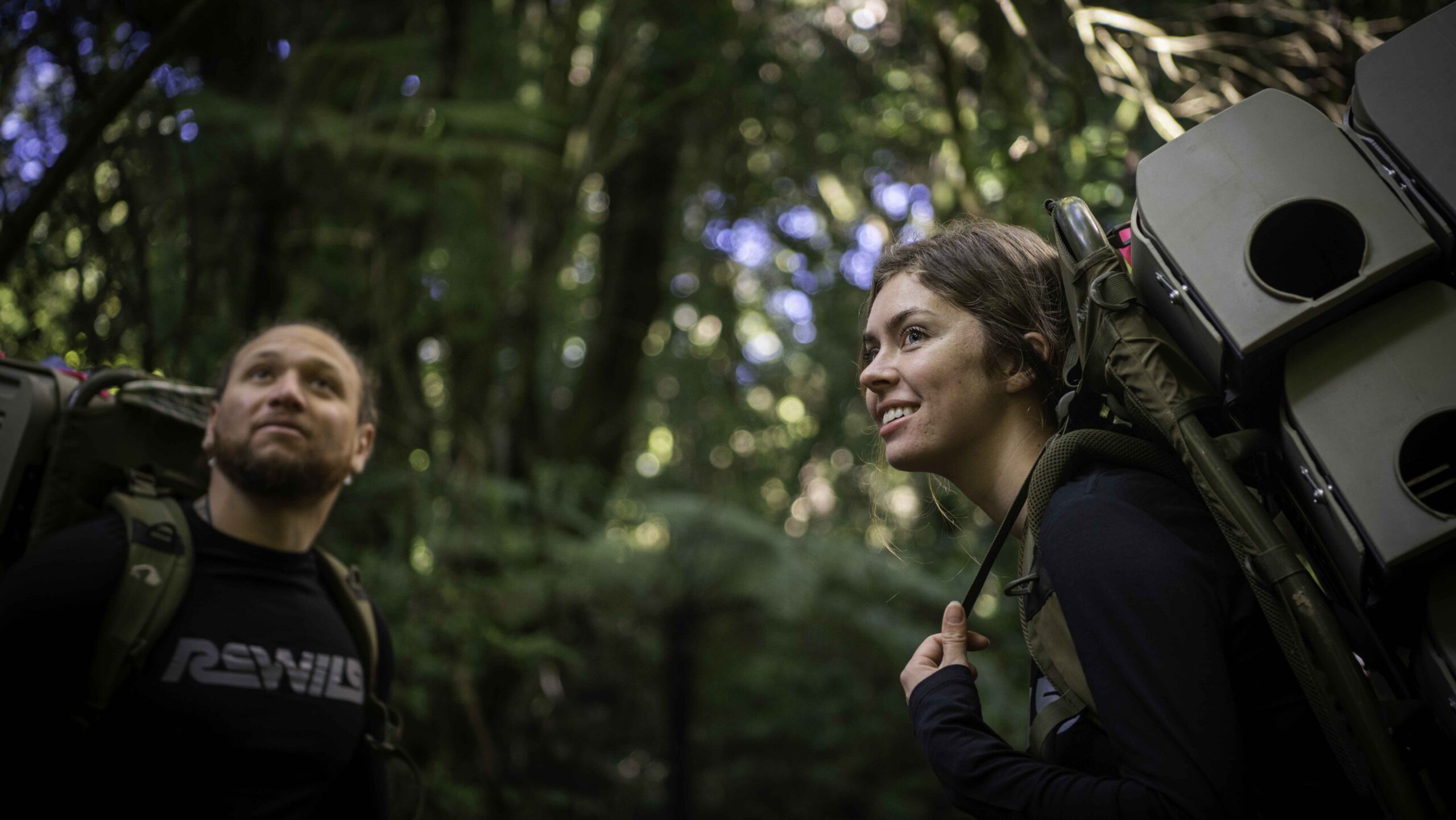
The next time you’re taking a walk through the bush, listen closely. Amidst the wind whistling through the native trees, the birdsong and the babbling of a nearby stream, you might soon hear an F-Bomb.
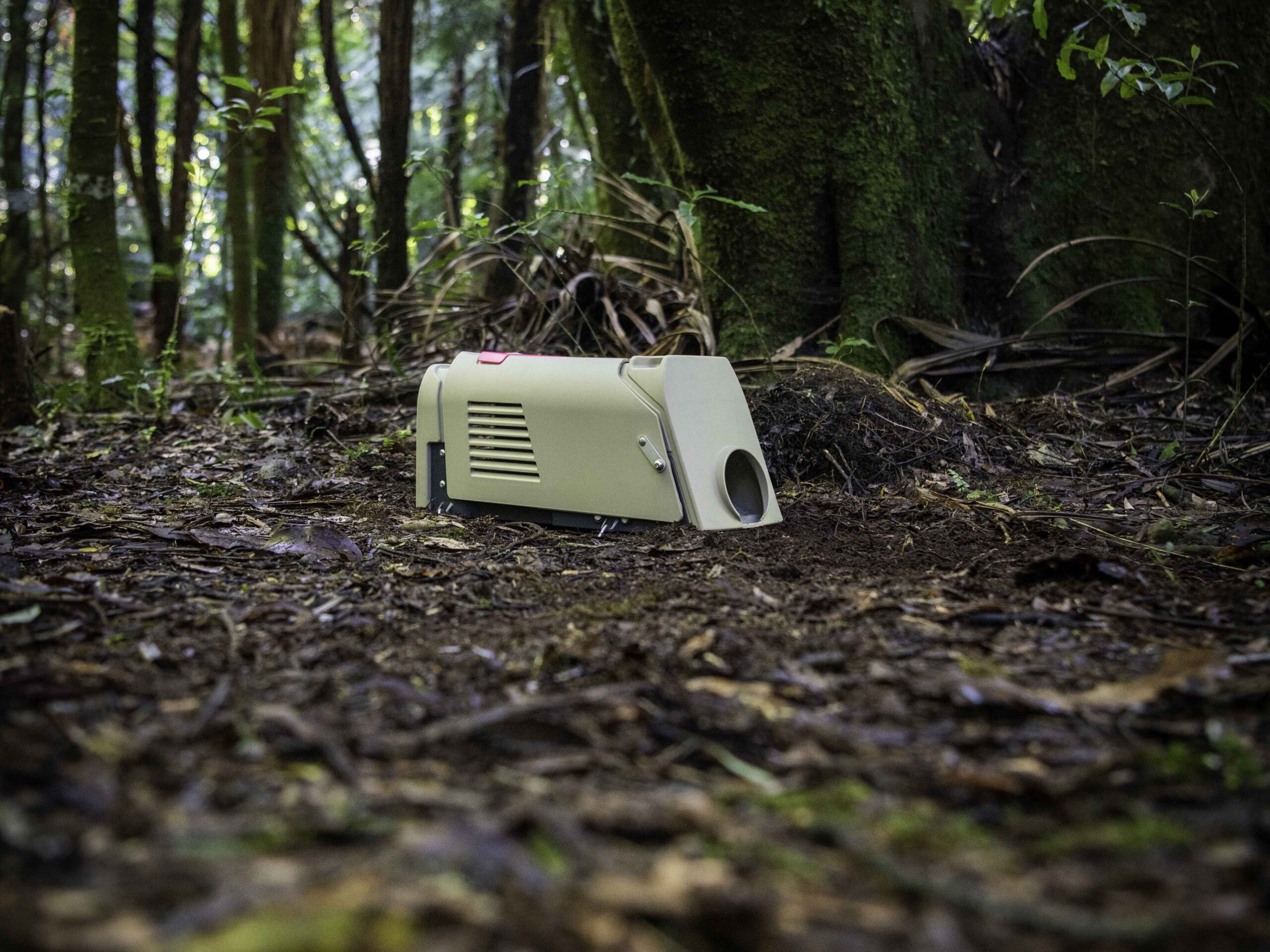
One of the latest in a new generation of predator traps, Rewild’s ‘F-Bomb’ builds on the success and dependability of the near-ubiquitous DOC 200 and DOC 250 traps set throughout the motu.
The Taranaki-based company recently marked the achievement of meeting the National Animal Welfare Advisory Committee (NAWAC) guideline for ferrets, stoats and Norway rats and expects to pass the test for ship rats shortly. Meeting the standard means the F-Bomb can dispatch those predators consistently and humanely, minimising their suffering.
Rewild founder and director Nick Jones says the journey to get NAWAC approval was lengthy and sometimes challenging. But it made for a better end product.
“It’s a really robust test, and it certainly aids in making your trap much better – improving the performance, the reliability, and the predictability of the trap,” Nick says.
It took around 13 tries to pass the NAWAC approval for ferrets.
“It was a lot of learning and [mistakes] along the way, but that’s part of product development,” the industrial designer says. “I’m very okay with being in that space of not knowing what your result’s gonna be and iterating your way to a solution.”
The origins of the F-bomb actually began around 15 years ago.
Nick was involved in trapping and noticed some of the devices’ “rudimentary” nature. As an industrial and product designer, he says he thought about how to take what had been successful – the DOC 200 and DOC 250 traps – and improve on it.
“It was really around how to make a better mousetrap,” he says.
The F-Bomb is lighter than the traditional wooden DOC traps, and it’s safe to service and set without any specialist training.
Nick believes introducing the F-Bomb into a broader ecosystem of traps and other tools is the key to reaching the country’s predator free goals. He says creating a trap that’s simple and easy to use can make it more accessible for the wider public to play their part in conservation.
“There’s a whole cohort who want to be involved in conservation. One of those barriers is actually the operation of dangerous devices and people aren’t really technically competent or physically capable of doing it.
“So it’s really just breaking down one of those barriers to participation and conservation outcomes,” Nick says.
He says one day he’d love for anyone walking by a sprung trap in the bush to be able to clear and reset it, ready for the next predator.
Like all tools, trappers need to be conscious of tools accidentally affecting non-target species like native birds. Caution needs to be taken and risks identified for the native species in your area interacting with the trap.
Made locally, trapped nationally
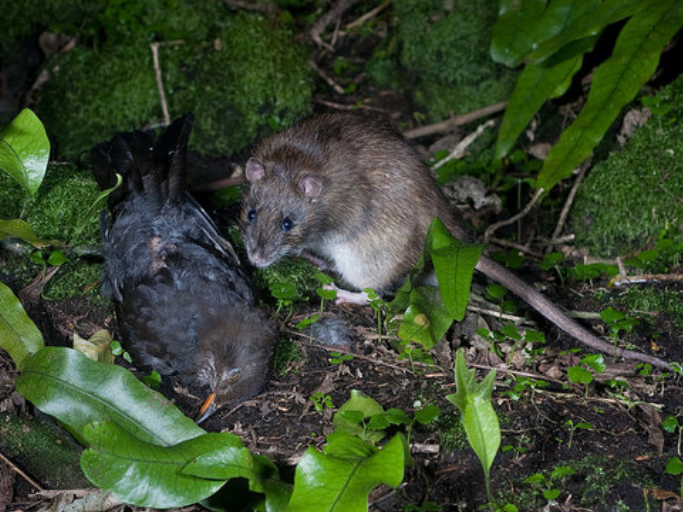
It was in a small, nondescript building in the Taranaki town of Inglewood, that the name for the F-Bomb was first dropped.
As part of quality assurance testing, the trap was set up on an automated rig so the team could better understand how many times it could be set off during its lifecycle.
“We ran like 5000 cycles on a production unit here and just kept dry firing it all day. It just sat in the corner and ran day in, and day out. People would come and go and, on more than one occasion, we’d be standing there talking away and the thing would go off a few metres away.
“People would be like ‘f***, what’s that?’ And we just started laughing,” Nick recalls.
The name stuck.
What’s also stuck is the desire to keep manufacturing the F-Bomb locally.
Despite the challenges of domestic manufacturing and the allure of potentially cheaper production in Asia, Nick says there are benefits to staying local, including shorter supply chains, no shipping delays, better quality control, and local job creation.
“I’d like to produce them cheaper, but at the price we’re producing, for now, it’s marginal. It’s certainly not some great bloody cash machine.”
The small team is close to producing its 500th unit. Following a significant investment into the plant, equipment and research and development, it has an initial goal of making the business financially sustainable. Longer term, Nick says he’d like to re-invest any surplus into future innovation and improvements.
“Anyone who’s developed a mature product will tell you that you start with a product, but they evolve with the market and over time and as you learn about those products when they’re in the field – they get better and better over time.
“We’d all be driving around in 1970s Corollas if products didn’t get better and better every time,” Nick laughs.
True to his product designer roots, Nick has already identified and implemented improvements to the F-Bomb.
“There’s always room for evolution.”