A swarm of drone aircraft appears over the horizon and spans out over a remote, unfenced wilderness area – one of many such large, open sanctuaries. The swarm is here for its regular monitoring visit and the drones spread out and begin collecting data with their many types of tiny sensors. Onboard 3D sensors map the vegetation and analyse water health. Tracking sensors can locate and identify monitored birds – even if they’re nesting in burrows.
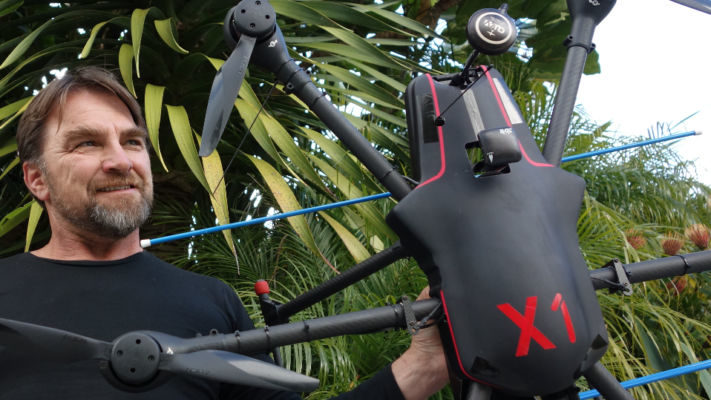
Thermal imaging sensors identify another moving form. Is it rabbit, rat or stoat? The distinctive movement patterns, analysed by computers back at base, reveal it to be a rat. GPS coordinates are recorded and will be followed up with predator control.
Mission quickly accomplished, the drone swarm returns to base until its next survey, but still the sanctuary is guarded. A hybrid airship is tethered at high altitude. Its long endurance means it has long-term relay capability for simple monitoring. The rarest of the rare species in this remote sanctuary have each been fitted with their own tiny ‘fitbit’ monitoring health, heart-rate and how far each individual is travelling.
What is its territory? How far is it travelling for food? Is it relatively home-based, perhaps sitting on a nest? Movement of each individual can be monitored long-term in real time.
Futuristic? The future is closer than you might think. Amazingly, the technological capability already exists – and sensors are getting smaller, more lightweight and cheaper all the time.
Philip Solaris is one New Zealander leading the way in those developments. His robotic craft company X-craft recently won a $25,000 WWF (World Wide Fund for Nature) ‘Conservation Innovation Award’ for its work on predator detection and eradication. It’s cutting edge work. He’s had interest from as far away as South Africa where the technology may one day be used to fight rhino-poaching – and it has huge potential here in New Zealand.
“There’s been a revolution in sensors,” says Philip. “There’s a massive contribution that robotic systems can make. It’s not just the aircraft, but the sensors have shrunk so much. Costs and size are rapidly decreasing.”
Size is important. Sensors need to be small to fly. So what are these sensors capable of? Take, for example, something called synthetic aperture radar.
“Infra-red falls down with looking through trees, but there’s sensor technology to help that issue,” says Philip. “Synthetic aperture radar can work with trees, fog and snow. It’s expensive currently but it’s getting smaller and cheaper.”
The original impetus for Philip’s robotic craft research and development was actually not conservation, but the 2010 Defence Review.
“We were looking at solutions for blue water monitoring – fisheries protection and border control. New Zealand has a huge Economic Exclusion Zone (EEZ), a large proportion of it given by the United Nations to New Zealand to protect and enforce. We could potentially lose it if we weren’t protecting and enforcing. There’s also search and rescue.”
Such a large coastline and EEZ isn’t easy or cheap to monitor.
“The airforce has aging aircraft and finance issues. I had done a series of papers on potential threats to industry. Things are only going to get worse – economic issues, resource issues. We looked for solutions in the robotics industry – seacraft and aircraft. The only viable solution is to utilize brainpower and robotics.”
As part of that process, Philip realised there were similar issues and big problems in the conservation field.
“There’s a lot of crossover with wildlife protection, reintroductions and the economic damage to conservation.”
Robotic craft are not restricted to land-based conservation. Semi-submersible craft also have potential for monitoring lakes, waterways and coastal habitats – helping identify toxins and weeds in streams for example.
Search and rescue is another area where robotic craft can be utilized to save time and potentially save lives. Rather than a search team risking their own lives and spending precious search hours crossing a swollen river to search a far bank they could search that bank with robotic craft in a fraction of the time. Examples such as this are often discovered when X-craft’s researchers and developers join Search and Rescue personnel in the field to see the way they work and the problems they face.
“We learn what’s important,” says Philip. “We always do field work, not just calculations. You learn a lot of stuff that you can’t do in the lab. And there’s a big reward in seeing robotic craft solve big issues for people.”
Philip says that it’s important to always be mindful of use.
“Cost and simplicity are important. It needs to be intuitive to use – for example, have the ability to automatically take-off and land. We aim to make very simple tools give a much bigger data set. Researchers can get an increased knowledge and range of data about an animal’s habitat for example, to get a broader, more holistic understanding of a creature. They can get more information for their dollar.”
It’s also important to approach each problem-solving challenge with an open mind.
“We review the method – how things are done – as well as the technology. If we can, we will try to tap into existing hardware, but it may not be the most efficient way to solve a problem. There may be huge potential from making a fresh start. We also need to integrate with how people work in the field.”
It can be quite a mind-change – a new way of thinking for people.
“People often have a thinking approach of a ‘single tool at a time’,” Philip explains. “But that’s old-fashioned. We can use multi-systems – swarm methodology. We can look at an area with a bunch of aircraft that ‘talk’ to each other.”
That swarm methodology not only has implications for future monitoring of New Zealand’s vast conservation estate. It also has huge benefits in a Civil Defence emergency response such as the Christchurch earthquake.
“There was no air cover for the first 24 hours after the Christchurch quake,” Philip says. “We could use 20 aircraft and a coordinated methodology and cover the city in a couple of hours. It could have sped up the recovery operation by days or even weeks.”
That’s not just the future we’re talking about. That monitoring capability is already here – and thanks to innovators like Philip and the X-craft research and development team, we are discovering new and better ways to use it.